09/2020 | SPECIALIST ARTICLE
Swiss army knife among blenders
Conventional agitators move the liquid in the container horizontally. But horizontal rotation is not effective. The liquid circles in the tank like in a carousel, and its inertia hinders vertical mixing. A Jetstream mixer offers many advantages over these agitators.
The problem of conventional stirrers can be demonstrated most easily with an example: In a process tank, a small amount of a pasty liquid is to be mixed into a low-viscosity, lighter liquid. The stirrer is started and the liquid begins to circulate. The paste is added, sinks to the bottom and also begins to circulate - the light liquid at the top circulates quite quickly, the heavy liquid at the bottom hardly moves at all. The operator reduces the speed so that the agitator does not stir in too much air. He observes a rapid rotation on the surface and is satisfied.
After 30 minutes, a check is made to see if mixing is complete and it is determined: No, the distribution is not homogeneous. Further stirring is required until an acceptable result is achieved. Batch protocols often contain mixing times of 30, 60 or even more minutes. Is this normal? No, such times are an indication that the mixer cannot mix homogeneously at all! If a process tank in which media have to be intensively mixed together is not homogeneously mixed from top to bottom within three minutes, the mixer is unsuitable.
Stirring is not enough
Agitators with open rotating rotor blades always circulate the liquid horizontally. In addition, they are usually installed in the middle of the tank - the worst position with regard to the rotation of the liquid.
To reduce the horizontal rotation of conventional agitators, baffles can be installed in the tank. But behind these baffles there are dead zones in which no mixing takes place at all. And these areas are also particularly difficult to clean.
Conventional agitators also have three other problems: firstly, there is almost no movement at the bottom of the tank, below the axis of the agitator. Secondly, there is a turbulence at the top of the liquid surface around the agitator shaft. This introduces unwanted air into the liquid. Furthermore, due to the lack of vertical circulation, they have difficulties when mixing solid suspensions, as solids have a tendency to sink. Terms such as "90% criterion", "two-second criterion" and "complete suspension" have been introduced. These terms mean nothing other than that the suspension is not really homogeneous, instead the suspension is described as "complete" when 90 % of the total mass is suspended or when the solids are not at the bottom for more than two seconds. Slow and ineffective agitators extend the process time, block the equipment and operators for an unnecessarily long time, limit the batch size and reduce the possible quality of the end product.
The Jetstream mixing principle
ystral relies on Jetstream Mixers because they always achieve very fast, complete and homogeneous mixing. The rotor of the Jestream Mixer is located in a stationary stator. The stator prevents the surrounding liquid from rotating and directs the flow of liquid directly to the bottom of the container. There, the flow is divided and directed upwards. At the surface of the liquid, the flow is directed back to the mixing head. This creates a consistent vertical circulation. Two mixing principles with different effects are combined: the effective laminar macro-mixing of the entire container contents and the highly turbulent micro-mixing during the passage of the mixing head. Laminar mixing alone, as known from some flow-optimized propeller mixers, produces movement with low power input, but not effective mixing.
When using a Jetstream Mixer in a process tank, one typically observes a movement of about 0.3 to 0.5 m/s at the liquid surface - directly from the side where the liquid comes up to the side where the liquid goes back down to the mixing head. At this speed, it only takes 20 to 30 seconds to mix the entire tank from bottom to top and back again in a 10,000-liter tank with a diameter of 2 m and a fill level of 3 m, for example. The liquid flow therefore passes through the turbulent zone in the mixing head two to three times per minute.
Jetstream Mixers are always positioned eccentrically, i.e. outside the center of the tank. For larger tanks, they can also be installed from the side or from below. It does not matter whether the tank is high or low, round or square, upright or horizontal. The mixing head is installed close to the floor. This means it can be used at full capacity at any fill level. An example: You want to start a batch with the smallest quantity and highest concentration and then dilute it by adding liquid - no problem at all for the Jetstream Mixer, unlike the agitator.
Jetstream Mixers in practice
Normal storage or maturing tanks are a wide field of application for theJetstream Mixers. In these tanks, the product must be kept homogeneous and protected from separation such as sedimentation or flotation. In these applications, there is no intensive mixing of media and no microturbulence is required, only homogeneous distribution and slow movement. For these applications, the Jetstream Mixers is equipped with a non-turbulent marine impeller. The same head is also used for heat exchange applications (heating, cooling).
Products that tend to agglomerate require perma-nent dispersion to prevent this. Turbulence alone is not enough. For these applications, the Dispermix - a combination of mixer and disperser - is the ideal tool. With the Dispermix, the outer part of the liquid flow is passed through the dispersing zone. By using this machine, the dissolving time of resins, thickeners or polyvinyl alcohol can be reduced to 10 %. The dissolving of cellulose ethers is reduced from hours to minutes.
Even more intensive dispersion combined with the advantages of Jetstream mixing in a single machine is possible when using the High Shear Dispermix. This machine can be used for the production of emulsions or dispersions with very fine particles.
Jetstream Mixers with the additional designation "Multipurpose" can be equipped with all three mixing heads. The tools are interchangeable. This makes the systems future-proof in the event that the task changes. In all cases, homogeneous, complete mixing is achieved within a few seconds.
www.prozesstechnik-online.de
Search term: ystral
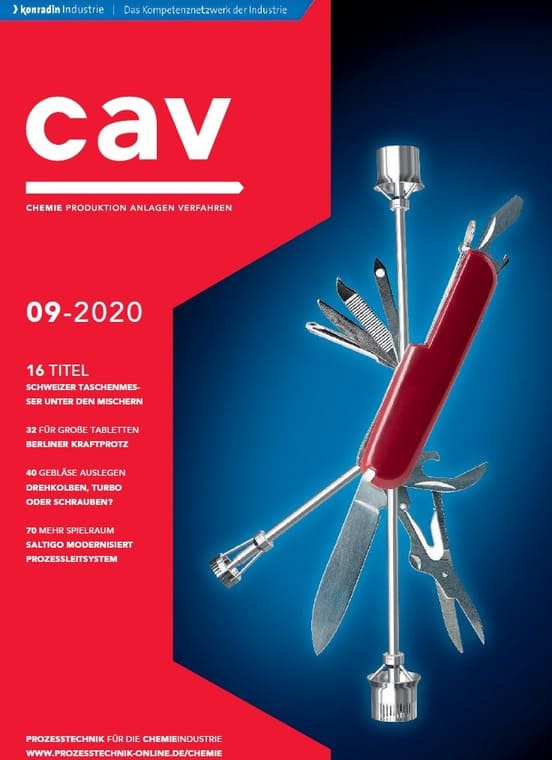
Article preview "Swiss Army Knife Among Mixers
Magazine: cav
Issue: 09/2020
Author: Dr. Hans-Joachim Jacob
About ystral
With our extensive knowledge and many years of experience in process and application technology
we offer targeted, customer-oriented solutions across all industries
- from laboratory equipment to production machines or systems.
We work with you to develop concepts and implementations for your individual applications, which
mean an immediately realizable and quantifiable added value for you.